Celda de soldadura robotizada con flexibilidad incorporada
MAHA, líder mundial en suministros de equipos para talleres, ha puesto en funcionamiento un sistema de soldadura totalmente robotizada que establece nuevos estándares en términos de flexibilidad en su sede corporativa en Haldenwang (Alemania). Se han establecido programas para más de 150 juntas soldadas después de un año de intensa actividad, con una tendencia ascendente continua.
MAHA es uno de los líderes mundiales del mercado en talleres y equipos de prueba de vehículos. La compañía, fundada por Winfried Rauch en Allgäu en 1969, ha crecido rápidamente para convertirse en un competidor global con una fuerza laboral mundial de más de 1.200 empleados, así como 150 agencias y 17 filiales internacionales.
En Haldenwang, alrededor de 750 empleados producen la gama completa de equipos de taller, desde bancos de pruebas y plataformas elevadoras de vehículos hasta varios tipos de equipos de prueba para automóviles, vehículos comerciales, motocicletas y vehículos especiales. Los talleres y las organizaciones de prueba de todo el mundo valoran la calidad superior de los productos que tienen una excelente reputación de durabilidad y fiabilidad.
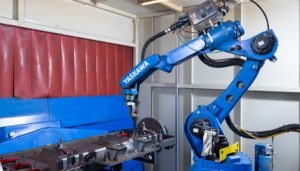
Pequeños lotes de 10 a 100
Erich Schmölz, jefe del departamento de soldadura robotizada de MAHA, resume lo que significa este compromiso con la calidad de producción: “En el sistema de robot debemos producir juntas de soldadura en pequeños lotes y con una calidad absolutamente reproducible. En el caso de nuestras plataformas elevadoras de camiones, por ejemplo, que se ofrecen con una carga útil máxima de hasta 60 toneladas, las vidas humanas dependen de la ejecución correcta de las juntas de soldadura. Los requisitos impuestos a los resultados de soldadura en las pruebas de calidad son, según la relevancia, estrictamente correspondientes”.
Calidad superior acompañada de la máxima flexibilidad: MAHA ha logrado esta «cuadratura del círculo» con un innovador sistema de soldadura totalmente automatizada concebido e implementado por los expertos en soldadura de Yaskawa en estrecha colaboración con los especialistas de MAHA en un sistema llave en mano que ahora opera en Haldenwang.
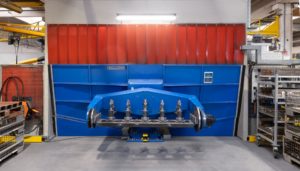
Diseño y construcción de un sistema de soldadura robotizada llave en mano
“La celda completa se compone principalmente de componentes estándar Yaskawa, por lo que los garantes reales de la flexibilidad son el robot de soldadura de alta velocidad Motoman MA2010 de seis ejes con controlador DX200 y el servo posicionador R2C de cinco ejes con dos estaciones para soldadura y carga paralelas durante el proceso», subraya Roland Hermann, gerente de ventas de Yaskawa.
Lo primero que llama la atención al mirar la celda es la inclinación aproximadamente de 15° del posicionador, lo que permite al operador colocar y sujetar las piezas de forma simple y ergonómica en el lado de carga. Este cambio de diseño también facilita el cambio de plantillas, es decir, los montajes para las variantes de componentes, lo que reduce los tiempos de reorganización a entre cinco y diez minutos.
Si el posicionador gira 180° en el área de trabajo, la inclinación crea una posición de trabajo elevada para el robot de soldadura, que por esta razón se monta en un zócalo. Una ventaja adicional de esta posición es la excelente accesibilidad del robot. En combinación, los cinco ejes del posicionador R2C y los seis ejes del robot, sincronizados de manera óptima por el controlador DX200, permiten una posición de soldadura perfectamente plana en todos los casos.
La programación offline aumenta la productividad
Lo que el especialista en soldadura Schmölz aprecia especialmente del sistema es la opción de programación offline: “A través de los datos CAD podemos programar cualquier conjunto de soldadura offline en paralelo a la operación, calcular con precisión los tiempos de soldadura, especificar secuencias de unión para garantizar retrasos mínimos, evitar colisiones y mucho más. En nuestras condiciones de operación con múltiples piezas pequeñas, la programación offline aumenta significativamente la productividad «.
A menudo, dos juntas diferentes se sueldan en el sistema de manera alterna, sin problemas con el posicionador de 2 estaciones. Sin embargo, se debe tener cuidado para garantizar que los tiempos de inserción sean más cortos que los tiempos de soldadura, ya que los tiempos de inactividad se deben evitar en MAHA. Es por eso por lo que la compañía optó por el Motoman MA2010. El robot de seis ejes tiene la reputación de ser resistente y puede realizar sus tareas en operaciones de turnos múltiples durante todo el día, siempre con la repetibilidad de trayectoria requerida. La máquina ofrece resultados de soldadura fiables, parte por parte, sin desviarse de las tolerancias dadas. El robot tiene un enfoque dinámico para su trabajo y garantiza el máximo rendimiento. Con una carga útil de 10 kg, tiene un alcance de 2.010 mm.
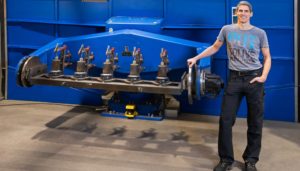
La fiabilidad y el conocimiento facilitan la decisión
No hace falta decir que antes de invertir en este sistema, los responsables de MAHA también consideraron los productos de otros fabricantes. Pero en sus deliberaciones siempre volvieron a Yaskawa. Uno de los factores contribuyentes fue sin duda que los robots de soldadura Motoman habían estado operando durante los últimos 22 años en la planta de Haldenwang con un alto grado de fiabilidad.
Pero además de este impresionante compromiso con la calidad, hubo muchos otros factores a favor de Yaskawa. Erich Schmölz nombra el criterio principal en pocas palabras: “Yaskawa tiene una increíble experiencia y puede diseñar sistemas de soldadura llave en mano exactamente según los requisitos del cliente utilizando muchos de sus propios componentes estándar. Nos beneficiamos de esta experiencia, así como del servicio ejemplar y la fiabilidad proverbial». La integración perfecta del sistema de soldadura en la producción y el funcionamiento sin problemas desde entonces puede considerarse como algo normal.
El rendimiento superior provoca una mayor inversión
Los operadores del sistema también están entusiasmados con su rendimiento. Aprecian especialmente la excelente accesibilidad del área de inserción generosamente dimensionada que está asegurada por el escáner de suelo, sensores fotoeléctricos y protectores de seguridad. Aquí hay suficiente espacio para depositar piezas con la carretilla elevadora. La operación simple y conveniente del sistema también facilita el trabajo diario. Esto también incluye un escudo antideslumbrante adicional en el posicionador, creando un área de soldadura completamente cerrada. Un potente extractor de humo de soldadura asegura que el aire del taller no esté contaminado.
En general, las altas expectativas de MAHA puestas en el sistema se han cumplido completamente en la práctica. “Este sistema nos ha permitido alcanzar nuestro objetivo principal de aumentar la flexibilidad de los procesos de soldadura con lotes pequeños. A pesar de la gran variedad de piezas, la productividad del sistema está al máximo nivel y nuestros planes para una segunda instalación idéntica ya están muy avanzados”, resume Schmölz.
Noticias relacionadas: