Granallado angular automatizado: innovación para una máxima competitividad e información del proceso
Sobre el cliente
Innovación en el tratamiento de superficies
Eseki es una empresa que se define bajo tres i: ingeniería, instalaciones e innovación. Ubicada en Etxarri-Aranatz (Navarra, España), se trata de una compañía de economía social –pertenece a sus trabajadores–, que además de proyectos en ámbitos como las instalaciones y el mantenimiento está especializada en el tratamiento de superficie, donde ofrece soluciones llave en mano que van desde la tecnología hasta los servicios.
Es en este ámbito donde Eseki ha hecho uno de los mayores aportes a la industria: el diseño y puesta en marcha del primer robot granalladora con 9 ejes de movimiento para granalla angular, flexible y modular, programado offline en 3D, que además ofrece mantenimiento inteligente. Fue precisamente sus amplios conocimientos del proceso del tratamiento de superficies, sumada a la apuesta de investigación y desarrollo en el ámbito de la robótica, que han convertido a Eseki hoy en una ingeniería capaz de diseñar grandes cabinas automatizadas para el tratamiento de superficies de piezas de grandes dimensiones –demandadas especialmente en mercados como el eólico o el siderometalúrgico a nivel nacional e internacional– ofreciendo también servicios de parametrización de nuevas piezas a tratar, además de tele mantenimiento, mantenimiento correctivo y preventivo.
Reto de negocio
Automatizar un proceso duro y complejo, obtener la máxima información
Tratamientos Algoi (Altsasu, Navarra) es una empresa dedicada al tratamiento superficial de piezas, especializada en procesos como el granallado, metalizado y pintado. Cliente de Eseki desde hace más de 25 años, Tratamientos Algoi está dedicada, principalmente, al acabado de grandes piezas para el sector eólico –torres y bujes– y de la industria siderúrgica.
Entre los procesos que ofrece se encuentra el granallado angular, que se utiliza para la limpieza de superficies, y que, al mismo tiempo, produce un micro picado en la pieza para una mayor adherencia de las siguientes etapas de tratamiento y pintura. “Al tratarse de un granallado angular, los sistemas automáticos no son válidos porque es un proceso altamente dañino para los equipos. Es por este motivo que siempre se opta por realizarlo de manera manual: el operario prepara la pieza y la granalla a mano”, explica Esteban Zeberio, gerente de Eseki.
Sumada a la dureza del tratamiento a la que se debe someter a los equipos, está la necesidad de máxima calidad del mismo. “Al tratarse de piezas utilizadas para procesos críticos –en este caso generación de energía eólica– se necesita un nivel de acabado estandarizado”, detalla Esteban Zeberio. Por lo mismo, la posibilidad de tener un estrecho control de todo el proceso, así como el poder estandarizar el proceso de granallado y de acabado de superficies en general, más que un deseo, representaba una necesidad. “A día de hoy las normativas en este ámbito, son muy claras en relación a cómo se debe trabajar la pieza para prevenir su deterioro, por ejemplo, pero la realidad es que el proceso lo realizan personas. La uniformidad del tratamiento queda hoy en sus manos”.
La calidad demandada, además, se lleva al límite al tratarse de grandes piezas con geometrías complejas y de diferente diseño y conformación: “Cuando trabajas con piezas de una variabilidad importante en cuanto a geometría y gran tamaño, la automatización se hace más compleja. Si a ello le sumas que se trata de piezas de 10, 20, 30 o 50 toneladas, la posibilidad de tener una solución automatizada se complica aún más”.
Por último, además de estas exigencias propias del proceso, se trata de un sector altamente competitivo, con numerosas exigencias por parte del cliente –situados en los segmentos TIER1, TIER2 y TIER3 de su sector– en cuanto a reducción de tiempos y de costes para ganar en competitividad: “la robotización en estos procesos va a ser clave para la mejora de la productividad”, comenta Zeberio.
Solución aportada
La primera cabina de granallado angular automatizada del mercado
La experiencia de Eseki en el sector de tratamiento de superficies fue uno de los tres pilares para el diseño de la solución de granallado automatizada para Tratamientos Algoi. A lo largo de los años Eseki se ha ido especializando en este proceso y, además, conoce muy bien el sector y las exigencias de competitividad a las que está sometido: sabían que era imprescindible automatizar.
El segundo de los pilares fue la decidida apuesta de I+D industrial hecha por Eseki. Con un departamento de investigación y desarrollo volcado a la mejora de los procesos de acabados de superficie de la industria, la primera fase del proyecto de Tratamientos Algoi, la correspondiente al prototipado, se llevó adelante a través de una línea de financiación del Gobierno de Navarra para la innovación en los procesos industriales. Eseki tenía una propuesta tecnológica atractiva, que daba respuesta a una necesidad del sector, capaz de automatizar un proceso que hasta la fecha siempre se había hecho de manera manual. Tenía, además, el apoyo de Tratamientos Algoi para aplicar la innovación.
El tercero de los pilares fue la colaboración con Yaskawa. La posibilidad de automatizar el proceso de granallado angular era una apuesta que tanto Yaskawa como Eseki, partners en diversos proyectos para el sector, habían valorado en repetidas ocasiones. De hecho, más allá de actuar como un proveedor de tecnología, la filial de la compañía japonesa en España ayudó a diseñar la solución que finalmente se ofreció al cliente, así como a buscar soluciones para la programación offline.
Sobre la base de estos tres pilares se realizó una primera solución de prototipo en el marco del proyecto de I+D financiado a través de la línea de ayuda del gobierno autonómico. Una vez acabada esta fase, Eseki realizó para Tratamientos Algoi el diseño personalizado de una cabina con sistema robotizado para el tratamiento superficial de bujes de aerogeneradores por granallado, con sistema CAD/CAM de 9 ejes, que incluye un sistema telemático totalmente automatizado de impulsión y recogida de granalla. Se trató de un proyecto llave en mano, en el que Eseki proporcionó desde el diseño a la puesta en marcha robotizada de la cabina.
Eseki aportó al proyecto un equipo de ingeniería con amplia experiencia en este tipo de procesos –diseño mecánico, electrónico, especialista en procesos, informáticos, eléctricos– y desde Algoi, además de Operaciones, hubo implicación directa por parte de la dirección de la compañía: “tenía que haber un compromiso muy alto a consecuencia de las demandas del proyecto. Implica una inversión de tiempo y de recursos importantes antes de ver los resultados. Ha supuesto un gran reto la robotización a través del CAD/CAM con el control para 9 ejes en un proceso como este”, comenta Esteban Zeberio.
La cabina automatizada se hizo realidad en cuatro fases. La primera fue de diseño e ingeniería, donde se definió el diseño mecánico, eléctrico, del CAD/CAM y la arquitectura de comunicaciones. La segunda fase fue de prototipado: implementación del prototipo y pruebas en un entorno controlado en las instalaciones de Eseki, sin trabajar aún con el granallado. En la tercera fase, se implementó la cabina en un entorno industrial con piezas reales. Fue en esa fase donde se pudieron confirmar y resolver los desafíos reales a los que se debía enfrentar la solución: el desgaste al que se sometía los componentes de la cabina, los tipos de recubrimientos que era necesario para proteger la instalación, las trayectorias necesarias para granallar la pieza, a qué distancia se ha de aplicar el granallado, qué velocidades, etc. Se readecuaron aquellas cosas que eran necesarias a través de la reingeniería y se pasó a la cuarta fase, la implementación final en casa del cliente de la primera cabina para granalla angular automatizada del mercado. En esta etapa, fue crítico no entorpecer la instalación de Tratamientos Algoi, tal y como explican desde Eseki: “Tienes una instalación automática para integrar en la línea global de producción. Implica comprender el global del proceso de tratamiento, hay que conocer el sistema y adecuar el funcionamiento del robot. La ingeniería no se limita sólo a la nueva celda de procesamiento de granallado, sino que se debe ampliar al global del proceso”.
A nivel tecnológico, la solución está compuesta por un robot GP25 Yaskawa de 6 ejes al que se le añadieron 3 servomotores Yaskawa controlados con la CPU del robot (x,y,z) que contribuyen a dar máxima capacidad de movimiento al robot en un pórtico con sincronización también a cargo de Yaskawa: “el controlador de Yaskawa tenía las prestaciones que necesitaba el CAD/CAM de 9 ejes que planteábamos”, comenta Esteban Zeberio. A través de un SCADA/HMI se controla todo el proceso y gracias a una pantalla táctil el operario selecciona la pieza que entra en la cabina y a la cual se le aplicará el proceso.
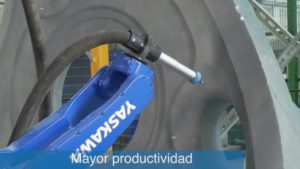
Resultados de la instalación y beneficios para el cliente
Mayor productividad, calidad y eficiencia en el consumo: competitividad máxima
A nivel de operaciones, el cambio ha sido sustancial. “Superior a nuestras expectativas”, tal y como detallan desde Eseki. “Se ha aumentado la capacidad de producción entre un 60% a un 80% pudiendo llegar a más dependiendo de la disposición de las grúas y demás elementos externos al proceso en la cabina”, explican. También se ha mejorado la uniformidad del tratamiento y con ello la calidad de las piezas, en primer lugar, por la mejora del proceso en sí mismo –“el proceso se realiza a mayor velocidad y por tanto se realiza un mejor picado con más posibilidades de granallado”– y en segundo, porque al tratarse ahora de un proceso automatizado, Eseki estructuró un entorno de analíticas capaz de dar seguimiento al proceso descubriendo las ineficiencias existentes: “Se descubrieron una serie de variables que se pudieron almacenar, como por ejemplo, a qué distancia es más efectivo el proceso. Ganamos nuevo conocimiento que se puede aplicar al proceso”. Estas mismas analíticas se utilizan para planificar el mantenimiento preventivo que necesita la instalación.
Otra ventaja importante es que se optimiza el consumo energético: “A menos tiempo de granallado más ahorro energético. La tarea que un empleado realiza en 5 horas de manera manual, el robot en la cabina la puede realizar en 1 hora 45 minutos”. También permite mayor continuidad de la producción: “no hace falta parar la producción para incorporar nuevas piezas a la línea. Los programas se cargan en online, o mediante un USB securizado, y ya se puede incorporar una nueva pieza con distintas dimensiones y geometría”. Para hacerse una idea de hasta qué punto se ha simplificado el proceso, basta con entender que cada buje tiene hasta 10.000 puntos de programación que se trabajan con SolidWorks en el taller y se cargan posteriormente en el sistema.
Asimismo, el tiempo empleado por el operario se optimiza: si antes se debía preparar la pieza por un grupo de operarios y luego realizar el granallado por otro, ahora la preparación de la pieza la hace un único operario mientras el robot está trabajando: “ahora, cada operario granalla más del doble de piezas en comparación a cuando se hacía de manera manual”. En este sentido, se ha eliminado la dificultad de contratación del personal ya que el trabajo duro e insalubre –que puede llegar a tener serios efectos sobre la salud si no se realiza con las medidas adecuadas– ahora lo realiza un robot mientras las personas están dedicadas a tareas de mayor valor.
En relación al trabajo de Eseki con Yaskawa, la colaboración fue completa tanto en el ámbito tecnológico como fuera de él. La cabina fue posible gracias al robot de altas prestaciones con una configuración preparada para soportar el entorno agresivo, apoyado por un controlador capaz de gestionar el sistema CAD/CAM propuesto: 9 ejes para máxima movilidad del brazo robótico con el objetivo de granallar de manera efectiva piezas con geometrías complejas. Comenta Esteban Zeberio: “no ha sido un proyecto fácil, nos ha costado alcanzar el punto de automatización que necesitábamos. Yaskawa tiene un desarrollo I+D que ha encajado muy bien con las necesidades del proceso de Tratamientos Superficiales”.
En relación al factor humano, el trabajo con el equipo fue fundamental: “no era un proyecto sencillo. Desde Yaskawa contribuyeron con ideas y un personal muy motivado para dar soluciones y soporte durante toda la instalación. Confío que, ahora que conocemos mejor el producto, podamos desarrollar bastantes más cosas”.
Para el futuro, el cliente ha descubierto las posibilidades que entrega la automatización y está estudiando cómo llevar más allá las mejoras implementadas en la cabina de granallado con la tecnología Yaskawa. Por parte de Eseki, ahora apostarán por impulsar el I+D en metalizado y después pintura. “La solución desarrollada para Tratamientos Algoi es aplicable en todos los sectores que necesitan un mayor control de los procesos de tratamiento. Además del sector eólico, puede ser altamente útil para la industria siderúrgica y la metalurgia”, explica Esteban Zeberio.
Pese a que en un inicio había cuestiones críticas que no se estaba del todo seguro se superarían –¿soportarán los componentes el ambiente altamente destructivo? ¿será rentable para el cliente el coste del mantenimiento vs. el beneficio de la solución? – con la solución ya en funcionamiento desde hace dos años se ha confirmado la gran innovación que representa para este proceso y para el sector en general. También queda evidenciado que Yaskawa es un robot muy robusto y con con gran durabilidad. “Hoy Tratamientos Algoi cuenta con una instalación innovadora con un retorno de la inversión muy interesante en términos productivos gracias a la correcta aplicación de la tecnología robótica. Un proyecto de éxito para todo el sector industrial”, concluyen desde Eseki.
Noticias relacionadas: