El mantenimiento y la puesta a punto de la maquinaria es uno de los gastos principales de la manufactura y la producción. David Messant, Director de producción en norelem, hace un repaso a cómo los componentes normalizados pueden reducir estos costes y hacer que las máquinas tengan el «menor mantenimiento» posible. Te contamos estas y otras conclusiones de norelem en este artículo.
Posiblemente no haga falta decir que el mantenimiento es un gran negocio. En algunos casos el coste del mantenimiento a lo largo de la vida útil de una máquina puede ser superior a la inversión inicial en la máquina misma si el mantenimiento no se gestiona de forma adecuada.
En el estudio 2018 Maintenance Survey de Plant Engineering, el 35% de los encuestados dijeron que gastan más del 10% de sus presupuestos operativos en mantenimiento, y otro 34% declararon que gastan entre un 5% y un 10% en mantenimiento.
Las compañías no pueden darse el lujo de dejar que sus máquinas funcionen hasta que se rompan ya que hacerlo supondría unas paradas no planificadas de sus equipos que causarían un daño importante en la productividad, los ingresos y los beneficios. Según IndustryWeek, las paradas no planificadas cuestan a los fabricantes industriales un importe aproximado de 50 mil millones de dólares estadounidenses al año, y un 43% de esta cantidad es debido a averías del equipamiento. Además de esto, las interrupciones no planificadas generan costes aún mayores debido al mantenimiento excesivo, reparación y sustitución del equipo.
La estrategia de mantenimiento de «utilizar hasta que rompa» está plagada de riesgos, de ahí que haya dos estrategias habituales, el mantenimiento preventivo y el mantenimiento predictivo.
Comparación de los enfoques de mantenimiento
El mantenimiento preventivo ha sido durante mucho tiempo el método de mantener las máquinas listas y en funcionamiento. Esta estrategia se basa en realizar la puesta a punto de las máquinas y sus componentes a intervalos regulares para prevenir que tengan averías imprevistas.
Elegir el mantenimiento preventivo reduce los riesgos de parada de forma dramática, pero implica un mantenimiento quizás excesivo de la maquinaria, y un sobresfuerzo de la mano de obra debido a la obligación de realizar comprobaciones regulares.
Por otro lado, el mantenimiento predictivo, si bien no es algo nuevo, ha despegado recientemente gracias a los rápidos avances de la Industria 4.0, las tecnologías conectadas y el IIoT (el internet industrial de las cosas). Mediante sensores y sistemas los ingenieros pueden ahora recoger grandes cantidades de datos de todo, desde ciclos y temperaturas de funcionamiento hasta vibraciones y ruido. Con este enfoque es posible actualmente predecir si los componentes de una máquina se deben sustituir o si la máquina tiene que ponerse totalmente fuera de servicio debido a la presencia de anomalías en los datos.
La contrapartida es que la configuración de un sistema de mantenimiento predictivo puede ser costoso al principio debido a la necesidad de tener un sistema completo IoT, sensores y software de seguimiento, junto con la formación de la plantilla para analizar los datos.
No importa el enfoque que se elija para realizar el mantenimiento de sus activos, todas las máquinas se pueden beneficiar del uso de componentes estándar para reducir los costes y hacer que el mantenimiento sea más eficiente.
Estandarización del mantenimiento de la maquinaria mediante componentes estandarizados
Unos de los grandes retos del mantenimiento es tener la plantilla con las competencias adecuadas para realizar las tareas necesarias de mantenimiento.
Es de sobra conocido que hay una brecha de competencias en ingeniería, y que cada vez menos negocios tienen personal dedicado de mantenimiento sobre el terreno, quizá porque es mucho más difícil encontrar el talento y retenerlo. En vez de eso, los contratos de mantenimiento tienen que subcontratarse con empresas externas. En el estudio de Plant Engineering se vio que mientras el 16% de los encuestados dicen no subcontratar ningún mantenimiento, el 44% subcontratan hasta el 20% de su mantenimiento global, y el 10% encargan al menos la mitad del mantenimiento a un proveedor externo.
Las competencias son el gran motivo de esto. El 46% de los encuestados por Plant Engineering dijeron que hay una carencia de competencias de mantenimiento entre la plantilla actual. Paralelamente, el 46% dijo también que un mantenimiento moderno exige competencias más especializadas.
Es evidente que la maquinaria se está haciendo cada vez más sofisticada, pero con el uso de componentes estandarizados en la fabricación de las máquinas se puede minimizar el problema de tener una plantilla de mantenimiento cualificada. Debido a los tamaños y versiones estandarizadas, los ingenieros no precisan tener un conocimiento previo concreto de componentes específicos y pueden sustituirlos simplemente cuando sea necesario.
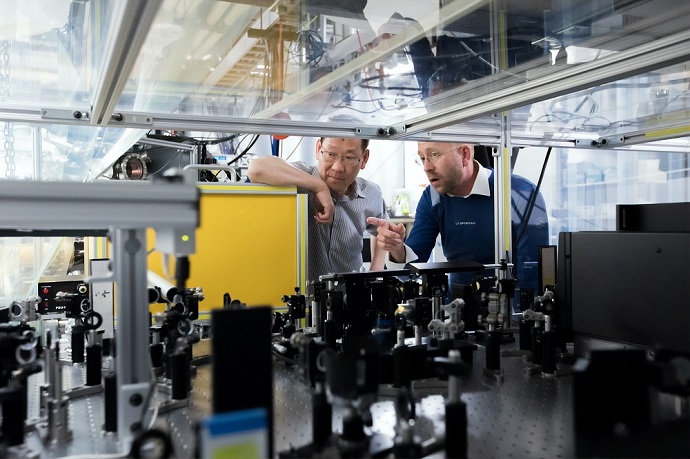
Elija componentes «sin mantenimiento»
Lo ideal de cualquier máquina sería que fuera «libre de mantenimiento» y no precise en absoluto de ninguna puesta a punto. Esto puede parecer descabellado aunque los ingenieros saben que el desgaste por uso es perfectamente normal y la naturaleza severa de los entornos industriales causa de forma natural la formación de depósitos de polvo, suciedad y residuos. No obstante, hay determinados elementos de la maquinaria que pueden estar hechos con componentes libres de mantenimiento para contribuir a la reducción del conjunto de reparaciones necesarias.
Un ejemplo de esto es el uso de ruedas dentadas y engranajes cónicos. Tradicionalmente estos engranajes se han hecho en acero, pero se pueden corroer con facilidad y su sustitución es costosa. Ahora, en cambio, hay versiones de plástico de estos engranajes, y norelem ofrece una gama de estas piezas de poco peso y a prueba de corrosión que precisan de poco o ningún mantenimiento. Estos engranajes son autolubricados y tienen un funcionamiento muy silencioso, además de poder instalarse en una amplia gama de aplicaciones y ofrecer una buena relación de precio-prestaciones que los convierte en una opción altamente rentable.
Hay una gran cantidad de otros componentes sin mantenimiento en la gama de norelem, como por ejemplo, los casquillos guía, otro componente ampliamente utilizado en ingeniería, del que norelem ofrece una versión hecha en bronce con insertos de grafito. Los elementos de fricción son libres de mantenimiento y resistentes al desgaste, con insertos de grafito que les proporcionan una lubricación duradera. Solo si las cargas son extremas y las velocidades de deslizamiento son superiores es recomendable una lubricación adicional.
Componentes estandarizados, rendimiento extraordinario
Una manera definitiva de reducir los requisitos de mantenimiento es elegir componentes que ofrezcan un alto rendimiento y calidad. Esto es particularmente importante en piezas que soportan grandes cargas, esfuerzos y fuerzas.
Un buen ejemplo de esto son los movimientos lineales automáticos y las piezas de trabajo de gran peso. Normalmente, estos movimientos someten a los componentes a elevadas fuerzas y condiciones extremas. Para este tipo de aplicación se recomienda que se utilicen unidades lineales para poner en movimiento grandes objetos ya que cuando se diseñan y personalizan correctamente pueden absorber las fuerzas máximas en todas direcciones. La gama de producto norelem incluye unidades lineales en longitudes estandarizadas con carreras de 200 a 1500 mm, además están disponibles en longitudes especiales bajo pedido para proyectos concretos.
En los sectores de manipulación de materiales, embalaje y agricultura los operadores también pueden ver incrementar sus costes de mantenimiento vertiginosamente debido a las exigentes funciones que asumen. Generalmente, en las máquinas de estos sectores se utilizan cadenas de rodillos simples y piñones, pero si se sustituyen por cadenas de rodillos dobles o triples y piñones se pueden reducir considerablemente los tiempos y los costes de mantenimiento. El rendimiento de las cadenas de rodillos dobles es 1,75 veces superior al de una cadena simple, y si se utilizan cadenas de rodillos triples el rendimiento es 2,5 veces superior. En THE BIG GREEN BOOK, el catálogo líder de norelem con más 60.000 componentes normalizados, información técnica y dibujos, se puede encontrar una completa gama de estos componentes junto con los piñones y tensores adecuados.

Reducción de los plazos y las paradas no planificadas
Para reducir los costes de mantenimiento hay que comenzar por anticipar las zonas de la maquinaria y los componentes donde es necesario realizar un mantenimiento periódico.
Haciendo esto e instalando máquinas con componentes estándar donde sea posible, las compañías pueden comenzar a superar los retos típicos asociados con esta disciplina de la ingeniería. Al no necesitar técnicos especializados para realizar el mantenimiento y al tener componentes de calidad y sin mantenimiento, los negocios comenzarán a ver gradualmente cómo el presupuesto necesario para el mantenimiento de los equipos comenzará a reducirse. Además, los componentes estandarizados deberían contribuir a la reducción de paradas no planificadas.
norelem tiene el 98% de sus componentes disponibles en almacén junto con fichas técnicas y datos CAD de todos sus componentes, lo que significa que los componentes que se averíen inesperadamente podrán ser sustituidos rápidamente, y las fábricas y la producción no tendrán que soportar una larga parada.
Para saber más de norelem, visite www.norelem.es
Noticias relacionadas